Typical Applications of Titanium Nitride (TiN) Coating
Titanium nitride coating is a versatile material that can be used in a wide range of industrial applications.
Medical Devices
In the medical industry, titanium coatings are critical for their biocompatibility, ensuring compatibility with body tissues and preventing adverse reactions. These coatings are primarily used in orthopedic implants, such as hip and knee replacements, where durability and corrosion resistance are critical for long service life.
Titanium is also used in dental implants and surgical instruments because of its ability to withstand repeated sterilization without degrading. Additionally, titanium’s antimicrobial properties help reduce the risk of infection, making it an important consideration for surgical and long-term implants.
Automotive Components
The automotive industry benefits from titanium nitride (TiN) coatings on parts like gears, bearings, and engine components. These coatings reduce friction and wear, extending the life of these parts and improving vehicle performance and reliability. Titanium’s thermal stability is particularly advantageous in the high-temperature environments of automotive engines, enhancing efficiency and reducing maintenance costs.
Cutting Tools
In the manufacturing of cutting tools, TiN coatings are widely used. These coatings significantly increase the hardness and wear resistance of tools such as drills, milling cutters, taps, and end mills. As a result, cutting speeds can be increased, tool life can be extended, and performance in cutting various materials, including metals, plastics, and composites, can be improved. The increased durability and reduced friction also mean that tools need to be sharpened or replaced less frequently, leading to increased productivity and cost savings.
Decorative Finishes
TiN coatings are also utilized for decorative purposes due to their attractive golden appearance. They are suitable for consumer products like watches, jewelry, and architectural accessories, providing not only an aesthetically pleasing surface but also a surface that is more resistant to scratches and abrasions, thus maintaining the appearance of the item over time.
Aerospace Components
In the aerospace industry, TiN coatings are applied to components that require high wear resistance and the ability to operate under extreme conditions. These components include turbine blades, landing gear, and other critical aircraft parts.
Titanium’s unique properties help withstand the high pressures, temperatures, and corrosive environments encountered in aerospace applications, ensuring reliability and safety while significantly reducing maintenance requirements.
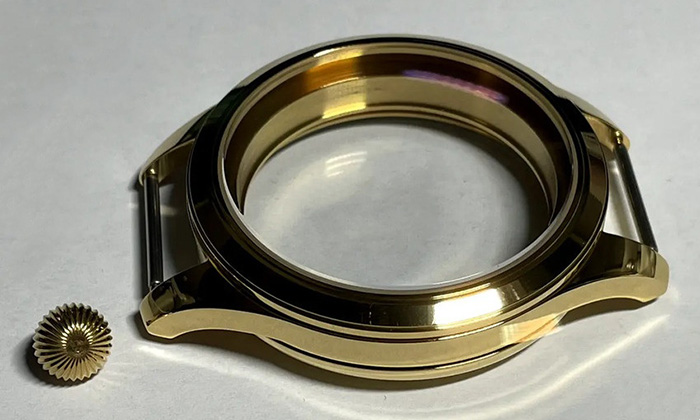